 |
Bed hanging and pillows. How about that electric blue microcord? |
Hurricane season officially began on June 1, and on Tuesday I officially had orders for 37 pillows in the studio- a regular spring storm of pillows. I like to hunker down and do them all at once as if they were one order.
I cut 29 of them to start with, adapting a quilt-making technique: using a straightedge and rotary cutter on a mat.
Once cut and marked to indicate front & back & bottom edge, I take the whole batch to the serger and serge the bottom edge where the zipper will go. This is tedious but best to get over with asap.
 |
All these for one client. Delicious colors! |
Back to the table, the cut pieces are arranged by sewing thread color, which generally is not the fabric color but the trim color.
Then time to dig in and start sewing. I'll sew the trim and assemble all the pillows of one sewing thread color, and then do all the zippers for that batch.
Zipper color is matched to the welting, not to the fabric. Two of these pillow were an unusual orange, with self-welt, and none of my zipper colors worked. I called
Alicia The Zipper Lady with my Zipper Emergency and she overnight-shipped the perfect matching orange zipper!
 |
For 3 different clients, but don't they look good together? |
|
They go to the serger and are serged all around and then turned and inspected. I want to catch any mistakes before I change the thread color on the machine.
If there are a lot of pillows, I'll stuff this batch, too, before moving on to the next- it's just a mind-game to have some of them all done! Feels like I'm making more progress than I really am.
For this bunch of pillows there was a lot of thread-changing, as you can imagine from the multitude of colors represented!
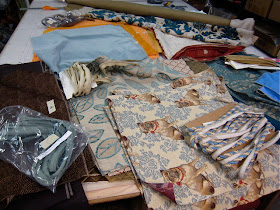 |
29 Pillows cut & bottom edge serged |
|
My personal pillow philosophy dictates tapered corners to minimize "ears" after stuffing. I equally dislike rounded corners. The tapering is done by eye: it's something you just have to have a feel for, like seam allowances.
I can't forget to mention the bed hanging in the top photo. Designed by Joshua at Fabu who always has an eye out for the most wonderful fabrics in the world, it's a fabulously delicious velvet embroidery on linen, with a burlap-like linen border that also forms the pocket. He also chose those wonderful fabrics for the pillows: the luscious teal velvet, with no trim; the quilted silk with electric blue microcord; and the same blue silk, lined with napped sateen and microcorded.
 |
Selecting zipper color is fun! |
The multi-colored batch of 14 pillows in the second photo are all designed by Liz at
Paris Interiors for her client, for two separate but adjacent spaces. The wovens are beautiful organic patterns like spirals and leaves. The thick solid velvets are soft and comfortable, and punchy with contrast welt. I especially loved the blue velvet with the orange-yellow velvet which I thought of as Electric Squash. You know how I like to name things- I called these pillows (in my mind, of course) the Allman Brothers Pillows- you know, "you're my blue sky, you're my sunny day"- you know, the blue sky and the yellow sun welting- oh well.
 |
Welt strips ready and waiting |
|
Back to zippers. Leatherwood Design Co pillows always get invisible zippers. The Zipper Lady has an excellent array of colors, and I keep almost all of them in stock.
I buy the zipper tape rolls with the slides attached- I cannot, cannot! put those slides on to save my life.
There is a special foot for installing invisible zippers, but I never use it- I just use a regular zipper foot and sew up as close as possible and frighteningly close to my left index finger.
Invisible zippers of course are not actually invisible, haha, but when properly installed they aren't noticeable. I've had customers complain that their pillows didn't have zippers- they didn't realize they were there!
With a chunky welt the zipper is more apparent because it's not possible to sew up real close to the zipper teeth, but if it's color-matched it's still better than a lapped zipper, I think.
 |
Silk pillows are lined with napped sateen |
One more thing, if you're still reading!- when we make silk pillows, we line them with napped sateen. We also serge all four edges of most pillows, except when serging is not beneficial (loose weaves sometimes fray more when serged) or for round pillows (serging constrains the shape). These are time-consuming techniques but, like color-matching the zippers, they are the details that make our pillows better.
If you're counting, there are 29 pillows shown, but two of them were photographed twice. I still have two more to make, silk Hermes scarves for the fronts and brown microcord and backing.
 |
How I taper pillow corners |
 |
Zippers match welt, not fabric |
 |
The Zipper Lady resolved the orange zipper emergency |
 |
Why I inspect for mistakes before changing thread color! |